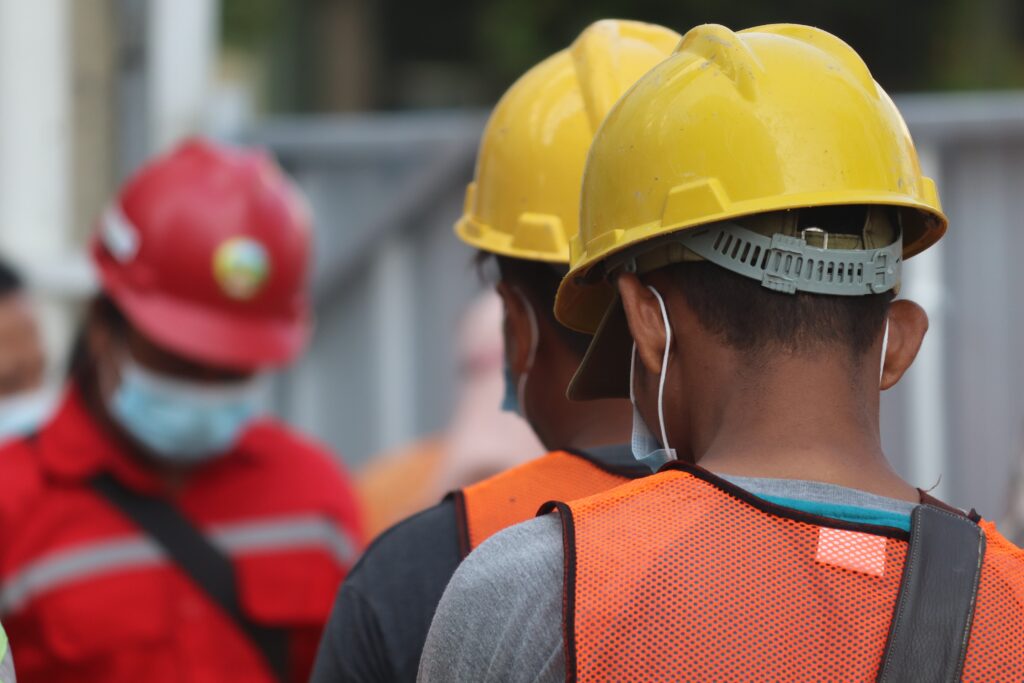
Forklift OSHA Violations – Forklifts have revolutionized material handling across various industries, increasing efficiency and reducing manual labor. From stacking pallets to transporting goods, they help streamline operations, ultimately saving time and resources. With their ease of maneuverability and the capability to lift heavy loads, forklifts significantly enhance productivity and efficiency, allowing businesses to meet operational demands seamlessly. However, although the benefits of forklifts are undeniable, this is a reminder to not cut corners when it comes to forklift safety. The Occupational Safety and Health Administration (OSHA) sets strict guidelines to ensure a safe working environment, and businesses must adhere to these regulations to avoid hefty penalties.
Failure to comply with OSHA regulations can result in significant financial penalties for businesses. At the time of this writing, serious violations can cost a business up to $15,625 per violation, a notable increase from the previous penalty of $14,502. The financial burden further escalates for failure to abate violations, potentially reaching $15,625 per day beyond the abatement date. Moreover, the repercussions for willful or repeated violations are even more severe, with businesses facing penalties of up to $156,259 per violation.
Common Forklift OSHA Violations:
Understanding OSHA violations related to forklift operation is paramount for businesses seeking to maintain a safe workplace and avoid penalties. Some common violations that businesses should be aware of include:
1. Operating a Forklift Without Certification:
OSHA mandates that all forklift operators must be certified to ensure they possess the necessary skills for safe operation. Failure to comply can result in fines and legal consequences.
2. Inadequate Use of Safety Equipment:
The absence or improper use of safety gear, such as protective eyewear, safety shoes, and harnesses, exposes operators to unnecessary risks. Providing the right equipment and ensuring its proper use is essential for a safe working environment.
3. Disregarding Speed Limits:
Excessive speed poses a significant risk, leading to loss of control and potential accidents. Businesses should enforce speed limits and provide visual reminders to prioritize safe forklift operation.
4. Driving with an Elevated Load:
Driving with raised forks increases the risk of items falling and causing injuries. OSHA emphasizes the importance of keeping the load low and forks are not sloping downward to maintain stability during operation. .
5. Proximity to Loading Docks:
Inching too close to loading dock edges can lead to tipping or falling accidents. Clearly labeling danger zones and conducting safety meetings are essential preventive measures.
6. Neglecting Pre-Operation Inspections:
Daily pre-operation inspections are mandatory, and neglecting them can result in accidents and equipment breakdowns. Regular training and reminders help ensure compliance with inspection requirements.
7. Not Removing Defective Forklifts:
Identifying and addressing defects during pre-operational inspections is crucial. Failing to remove defective forklifts promptly poses serious safety risks and violates OSHA regulations.
8. Failure to Provide Refresher Training:
Refresher training is necessary after accidents, observed unsafe operations, or changes in forklift types or workplace conditions. Periodic training sessions enhance operator skills and knowledge.
Forklifts undoubtedly play a vital role in the efficiency of warehouses, but their operation demands strict adherence to safety protocols. OSHA penalties for violations are substantial, underscoring the need for businesses to prioritize safety and avoid cutting corners. By investing in comprehensive training programs, regular inspections, and a culture of safety awareness, businesses can create a secure workplace while reaping the benefits of forklift-driven operational excellence. It’s not just about avoiding penalties; it’s about ensuring the well-being of the workforce and fostering a culture of safety that resonates throughout the organization. To learn about certifying your team or yourself, contact us today.